Reduce Underloading in Mining Operations: The Hidden Cost of Every Partially Loaded Truck
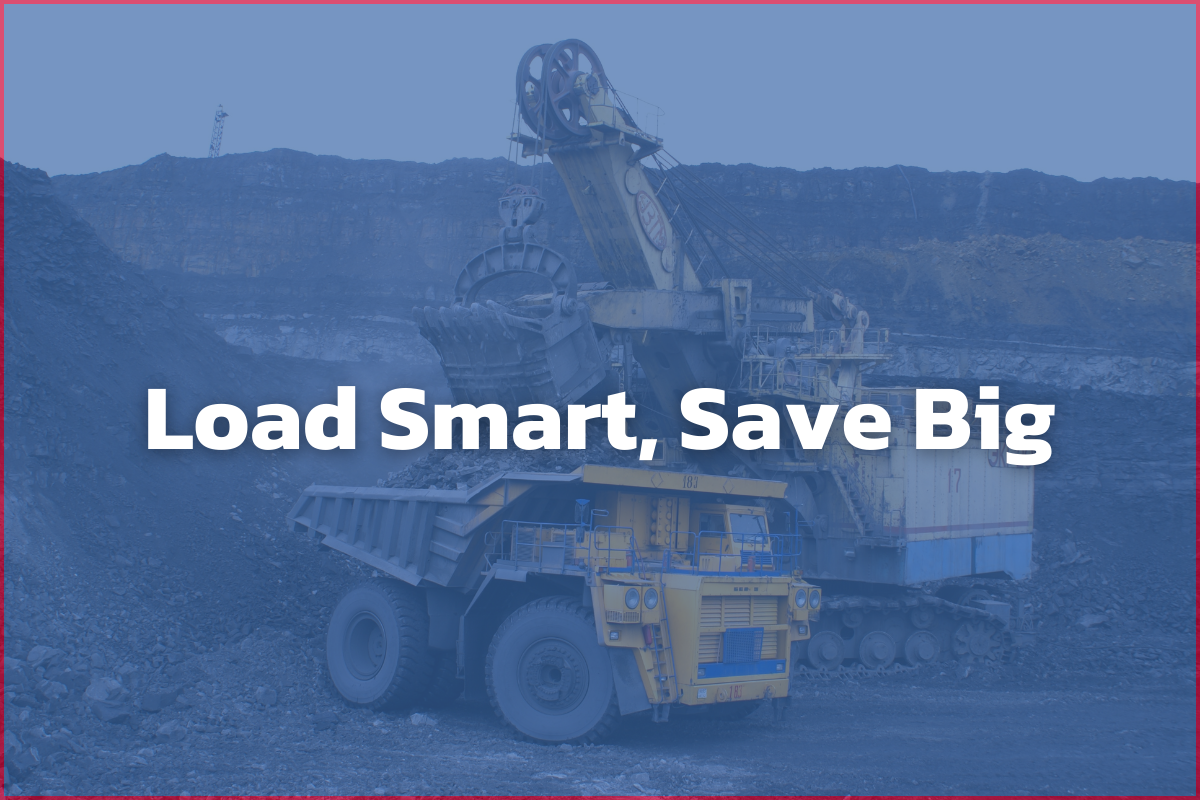
Looking to reduce underloading in mining operations and reclaim lost profits?
Underloading hides in the shadows and robs the effectiveness of many mine operations.
It occurs when haul trucks carry less than their rated capacity.
And when trucks carry less than their rated capacity, the result is lower productivity and higher costs with each and every trip.
In this guide, we’re going to cover 3 important countermeasures you can address to positively impact underloading in your mining operations:
1. We’ll define underloading.
2. We’ll explore why it’s important to avoid underloading.
3. And most importantly, you’ll want to keep reading to uncover actionable strategies.
We’ll cover the solutions designed to reduce costs, so you can stay ahead of industry trends.
What Is Underloading in Mining Operations?
Here’s the deal…
(And if you’ve been in the pit for more than 5 minutes, you already know exactly what I’m talking about.)
When your haul trucks run light, you’re literally leaving money in the dirt.
Your 100-ton beast is built to haul, what? 100 tons. (Yeah, I know… shocking math there.)
But when it’s only carrying 95 tons from the face to the dump, that’s pure profit staying in the muck.
Do the math on your production cycle – that’s 5 tons of payload missing on every haul. Multiply that across your fleet’s cycles, and you’re burning more diesel per ton than a greenhorn operator.
That’s exactly why veteran operations are working to reduce underloading in mining operations across their sites.
Why Does Underloading Happen?
There are 4 BIG reasons why underloading can occur:
- Carryback: Materials sometimes remain in the truck bed, which reduces the available capacity for each new load.
- Operator experience level and lack of training: Loader operators may avoid overloading and err on the side of leaving extra space due to lack of experience or training.
- Equipment mismatches: If a shovel’s bucket capacity doesn’t align well with the truck’s payload, consistent under-filling may occur.
- Lack of real-time data: Without immediate feedback on load weight or volume in real-time, loaders often “guess” a full load.
Reasons Why You Want To Reduce Underloading in Your Mining Operations ASAP
Fixing underloading sooner rather than later is very important for several reasons.
Wasted Capacity and More Trips
Every underloaded truck effectively carries “air” instead of valuable material. This problem multiplies over hundreds—or thousands—of cycles. This means requiring additional trips and severely limiting a mine’s output.
As Caterpillar’s research underscores in their handbook (p. 16-47), optimizing truck loading for fewer passes can dramatically enhance productivity and reduce fuel consumption.
Higher Operating and Maintenance Costs
Underloading doesn’t just waste capacity—it drives up your operating costs.
What do we mean by that? Extra trips burn more fuel and add unnecessary wear on tires, engines, and components. Even minor shortfalls in load capacity can lead to disproportionately higher maintenance and fuel costs.
Why?
Each trip consumes similar energy whether the truck is loaded at 70% or 100% capacity.
Lost Revenue Opportunities
A shortfall of 5–10% capacity on each haul can translate to losing thousands of tons of material movement per week.
In tight-margin markets, having a reliable quarry production monitoring system to optimize load volumes can spell the difference between profit and loss
By improving average load factors, many mines see a direct uptick in tonnage hauled per day. This translates to consistent production and more revenue.
After seeing how underloading drains capacity, drives up costs, and cuts into profits, you’re probably wondering: how can we tackle this challenge head-on?
Five Practical Steps to Reduce Underloading in Mining Operations
Addressing underloading typically involves a combination of technology, training, and continuous improvement.
Below are five proven steps to tackle the issue head-on, so you can save time and money.
1. Implement Real-Time Load Measurement
A reliable truckload scanner or onboard scale system can alert operators when a truck is under its capacity. Laser-based volumetric scanning solutions are particularly useful.
What is a truckload scanner, and why is it useful?
A truckload scanner is a device that uses laser technology to quickly measure the volume of material loaded into haul trucks.
As each truck passes under the scanner, it instantly calculates how full the truck is. And importantly, it also provides you with precise load data, so you can make smarter decisions to optimize your hauls.
See an example truckload scanner in action:
This helps loaders know immediately if operators need to add or remove material before the truck leaves the loading area.
This real-time visibility means loaders can top off trucks accurately rather than just guessing.
2. Train and Motivate Your Operators
Even the best technology won’t solve underloading if your teams don’t know how to use it effectively. Conduct periodic training sessions that focus on:
- Proper loading techniques
- How to improve mine hauling through better payload management.
- Understanding the real impact of underloading on the bottom line.
Encourage healthy competition among crews to maintain high load factors and reduce unnecessary space. For example, you might offer rewards to the crew that consistently achieves the highest average payload each month.
Rewards could be gift cards, team lunches, and/or recognition on a visible leaderboard.
Recognize improvements publicly and regularly share performance metrics. This motivates crews to load trucks more effectively, builds team spirit, and makes efficient loading a point of pride for everyone involved.
3. Fine-Tune Your Truck Loading Procedures and Equipment
Look for ways to standardize and streamline your loading cycle:
- Set Specific Load Targets: For each truck model, define a clear tonnage or volume goal.
- Sync Equipment Capacities: If a truck’s rated payload is 100 tons, align your shovels, excavators, or loaders so each pass contributes effectively toward that total.
- Minimize Carryback: Regularly clean or apply liners to truck beds to prevent material from sticking. Even a few tons of carryback can lead to consistent short-loading over time.
4. Monitor Fuel Costs and Overall Efficiency Of Your Hauls
Underloading can reduce efficiency just as much as overloading. With each trip, trucks consume fuel whether they’re full or not. Tracking the effects of overloaded trucks on fuel costs is common, but keeping a close eye on underloaded trips is just as important. Gather data on:
- Fuel used per ton of material moved
- Load factor per shift
- Maintenance expenses over time
When you notice problems like rising fuel costs or lower amounts of material hauled, check if underloading is the cause.
An industry report by the Canadian Mining Journal (2020) revealed that mines can boost efficiency by up to 15%. They do this by making sure trucks carry full loads every trip.
Picture a vast open-pit mine where trucks once ran at just 70–80% capacity, forcing extra trips and extra fuel use.
With improved loading practices, those same trucks now operate near full capacity. They can cut their trips from 100 to about 85 a day. They can save fuel, reduce wear, and speed up production.
For example, if each trip costs roughly $500, eliminating 15 trips per day can save about $7,500 daily. This translates to nearly $1.9 million in savings per truck annually over 250 operating days. Wild, right?
5. Embrace a Culture of Continuous Improvement
Modern mines produce a wealth of operational data—use it. By regularly analyzing load metrics, you can adjust training, schedules, and equipment usage to keep progress on track. A continuous improvement mindset helps you:
- Identify patterns in haul truck underloading
- Adjust loading targets based on material density changes
- Justify new technology investments, such as advanced scanning or autonomous solutions
Final Thoughts: How to Reduce Underloading in Mining Operations for Lasting Efficiency
By taking clear steps to reduce underloading in mining operations, you can improve hauling efficiency, move more material each day, and lower your operating costs.
Simple actions like using a truckload scanner to see load levels in real-time, improving loading methods, and training workers to fill trucks fully can help your mine save money.
Underloading might not seem obvious at first. But solving it is an easy and effective way to improve your mine’s hauling efficiency and productivity.
Need hands-on help to reduce underloading in your mine operation?
Advanced LiDAR technology helps mines accurately measure loads and boost productivity (…even if you’re in a challenging environment).
If you’d like to learn more about volumetric load scanner technology or get expert solutions for improving haul truckload accuracy. click here to contact our team.
Every haul matters.
Maximize each to stay competitive and profitable in today’s demanding mining environment.
Interested in learning how Wingfield can help your business?
Schedule a conversation with a wingfield specialist!
or call 423-698-0100